A Comprehensive Overview to the Refine and Advantages of Plastic Extrusion
In the large world of manufacturing, plastic extrusion emerges as a highly efficient and important procedure. Translating raw plastic right into continuous profiles, it provides to a variety of industries with its amazing versatility. This overview aims to elucidate the intricate actions entailed in this approach, the kinds of plastic appropriate for extrusion, and the game-changing advantages it brings to the industry. The taking place discussion guarantees to unravel the real-world impacts of this transformative procedure.
Comprehending the Basics of Plastic Extrusion
While it may show up complex at very first glimpse, the process of plastic extrusion is essentially basic - plastic extrusion. It is a high-volume manufacturing strategy in which raw plastic is melted and shaped into a constant account. The procedure starts with the feeding of plastic material, in the kind of powders, granules, or pellets, into a warmed barrel. The plastic is after that melted using a mix of warmth and shear, used by a rotating screw. When the molten plastic reaches the end of the barrel, it is forced via a small opening referred to as a die, forming it right into a preferred form. The designed plastic is then cooled down, strengthened, and reduced right into desired lengths, completing the procedure.
The Technical Refine of Plastic Extrusion Explained
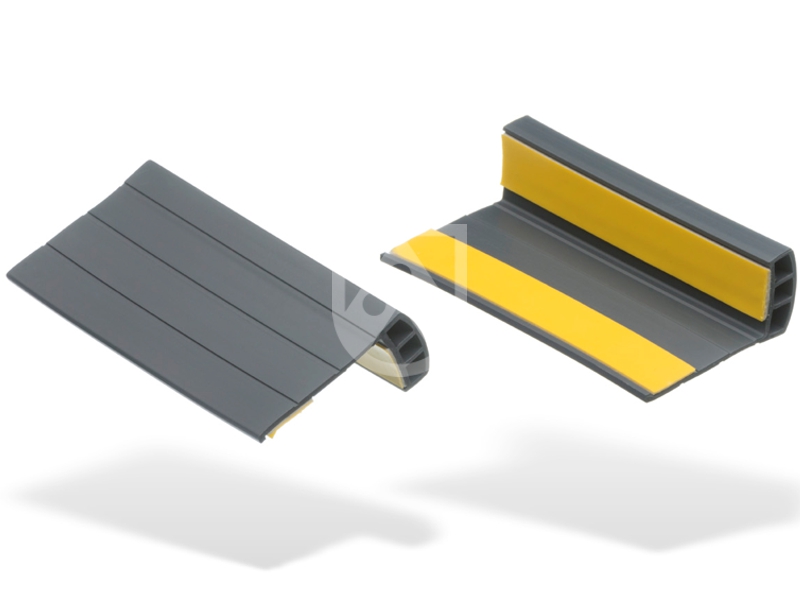
Kinds of Plastic Suitable for Extrusion
The selection of the ideal sort of plastic is a vital facet of the extrusion procedure. Various plastics offer special buildings, making them a lot more suited to particular applications. Polyethylene, for instance, is frequently made use of due to its low price and very easy formability. It provides superb resistance to chemicals and wetness, making it excellent for items like tubing and containers. Polypropylene is another popular option due to its high melting point and resistance to tiredness. For even more durable applications, polystyrene and PVC (polyvinyl chloride) are frequently selected for their stamina and durability. Although these prevail choices, the selection eventually depends upon the specific needs of the product being generated. Comprehending these plastic kinds can considerably improve the extrusion procedure.
Contrasting Plastic Extrusion to Other Plastic Forming Techniques
Comprehending the kinds of plastic suitable for extrusion leads the way for a broader conversation on how plastic extrusion piles up versus various other plastic forming methods. Plastic extrusion is unrivaled when it comes to producing continuous accounts, such as gaskets, seals, and pipes. It likewise enables for a consistent cross-section along the length of the item.
Secret Benefits of Plastic Extrusion in Manufacturing
In the realm of manufacturing, plastic extrusion offers many considerable advantages. One significant benefit is the cost-effectiveness of the procedure, which makes it a financially appealing production technique. Additionally, this method gives remarkable item flexibility and boosted production rate, thus enhancing general manufacturing efficiency.
Affordable Production Method
Plastic extrusion leaps to the center as an economical manufacturing method in manufacturing. This procedure stands out for its capability to generate high volumes of product promptly and efficiently, providing manufacturers with significant cost savings. The main price benefit is the capacity to utilize more economical basic materials. Extrusion makes use of polycarbonate materials, which are less pricey compared to ceramics or steels. Further, the extrusion process itself is reasonably simple, lowering labor expenses. In addition, plastic extrusion requires less energy than typical production approaches, adding to reduced functional prices. The procedure additionally decreases waste, as any kind of defective or excess products can be reused and reused, offering an additional layer of cost-effectiveness. Overall, the economic advantages make plastic extrusion a highly attractive option in the production market.
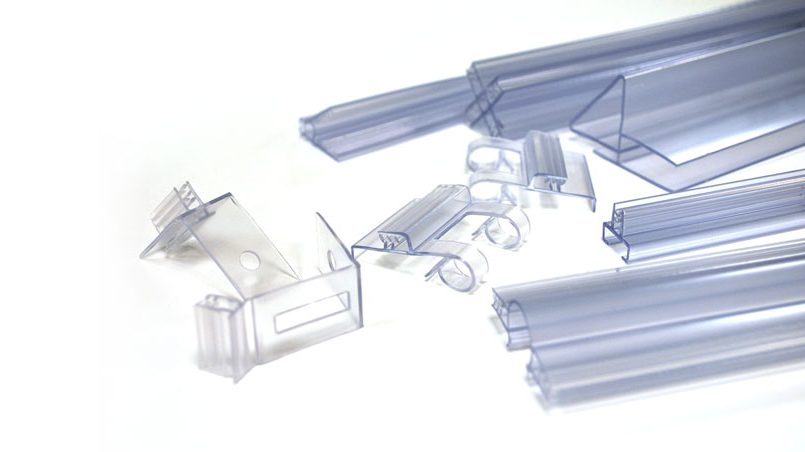
Superior Item Adaptability
Past the cost-effectiveness of plastic extrusion, an additional considerable benefit in producing depend on its superior product versatility. This procedure permits the development of a large variety of products with differing sizes, forms, and styles, from easy plastic sheets to intricate accounts. The flexibility is credited to the see here extrusion die, which can be customized to produce the desired item layout. This makes plastic extrusion an ideal solution for sectors that need customized plastic components, such as auto, building, and packaging. The capability to important source create diverse products is not just valuable in conference particular market needs yet additionally in allowing makers to discover new product with very little resources investment. Basically, plastic extrusion's item versatility fosters advancement while enhancing functional performance.
Boosted Production Rate
A significant advantage of plastic extrusion exists in its boosted manufacturing speed. Couple of various other production processes can match the speed of plastic extrusion. Furthermore, the capacity to keep regular high-speed production without sacrificing product high quality sets plastic extrusion apart from various other approaches.
Real-world Applications and Influences of Plastic Extrusion
In the world of production, the method of plastic extrusion holds extensive significance. The financial advantage of plastic extrusion, mainly its high-volume and cost-effective result, has actually transformed production. The sector is constantly striving for innovations in biodegradable and recyclable products, indicating a future where the advantages of plastic extrusion can be preserved without jeopardizing ecological sustainability.
Verdict
In conclusion, plastic extrusion is a extremely efficient and efficient technique of changing raw materials into varied products. It supplies numerous benefits over other plastic forming methods, including cost-effectiveness, high result, minimal waste, click over here and design adaptability. Its effect is exceptionally felt in different industries such as construction, auto, and durable goods, making it a crucial procedure in today's manufacturing landscape.
Delving deeper into the technological process of plastic extrusion, it begins with the selection of the appropriate plastic material. When cooled, the plastic is cut into the called for sizes or injury onto reels if the item is a plastic film or sheet - plastic extrusion. Contrasting Plastic Extrusion to Various Other Plastic Forming Approaches
Comprehending the types of plastic appropriate for extrusion leads the means for a more comprehensive conversation on exactly how plastic extrusion piles up against other plastic forming approaches. Few other manufacturing processes can match the speed of plastic extrusion.